炼钢渣量波动因素与控制策略分析探讨
该思维导图详细分析了炼钢过程中渣量波动的五大因素。首先,原料条件波动,包括铁水成分、废钢质量和辅料稳定性,直接影响渣量。其次,工艺操作的参数控制、造渣制度和温度管理也会造成波动。设备及生产条件如炉衬侵蚀和除尘效率同样重要。钢种特性和冶炼阶段差异进一步加剧了渣量波动,此外,外部环境和操作标准化水平也会影响最终结果。最终提出了一系列控制策略以优化渣量管理。
源码
# 炼钢渣量波动因素与控制策略分析探讨
## 一、原料条件波动
### 1.1 铁水成分变化
- 硅(Si)含量
- 每增加0.1%:渣量增加约15-20kg/t钢
- 磷(P)含量
- 升高需额外脱除:增加造渣剂用量
- 硫(S)含量
- 升高需额外脱除:造成渣量增加
- 温度波动
- 铁水温度低需补热,影响熔剂熔解速率
### 1.2 废钢质量差异
- 杂质含量
- 高油污、镀层等杂质
- 渣中氧化物及非金属夹杂物增加,渣量上升5-10%
### 1.3 辅料成分稳定性
- 石灰有效CaO含量
- 降低10%需多消耗15%石灰量,导致渣量增加
## 二、工艺操作波动
### 2.1 吹炼参数控制
- 供氧强度变化
- 从3.5Nm³/t·min提高到4.0Nm³/t·min,渣中FeO含量增加2-3%
- 终点控制偏差
- 碳、磷未达目标需补吹:每补吹1分钟渣量增加约5kg/t钢
### 2.2 造渣制度执行
- 碱度调整
- 碱度从3.0调整至3.5,需多加入约8%石灰
- 熔剂分批加入时机
- 前期石灰加入不足,后期需补加导致渣层不均匀
### 2.3 温度管理
- 出钢温度管理
- 超过目标值20℃时,渣中FeO含量上升1.5%
## 三、设备及生产条件影响
### 3.1 炉衬侵蚀
- 炉衬MgO-C砖的侵蚀
- 渣中MgO含量升高2-3%,需调整熔剂配比
### 3.2 喷溅与溢渣
- 转炉喷溅损失
- 一次喷溅损失渣量约3-8%
### 3.3 除尘效率
- 除尘系统抽吸效果
- 过强导致渣中细粉损失增加,渣量实测值偏低2-4%
## 四、钢种与冶炼阶段差异
### 4.1 钢种需求差异
- 超低磷钢(P≤0.008%)
- 需多次造渣,渣量比普通钢种高20-30%
- 不锈钢冶炼
- 需添加CaF₂或Al降低渣粘度,导致渣量增加10-15%
### 4.2 冶炼周期阶段
- 氧化期
- 渣量占全程60-70%
- 还原期
- 需要扒渣再造,导致渣量分段波动
## 五、外部环境与人为因素
### 5.1 环境温度影响
- 冬季车间温度
- 低温导致炉体散热快,间接增加渣量1-3%
### 5.2 操作标准化水平
- 操作员水平
- 经验不足可能导致超加熔剂5-10%,或误判终点
## 渣量波动控制策略
- 原料预混均质化
- 铁水预处理脱Si、脱P,控制入炉Si≤0.3%
- 动态模型优化
- 采用炉气分析+副枪技术实时调整造渣剂量
- 设备智能监测
- 激光测厚仪监控炉衬侵蚀情况
- 操作标准化
- 建立吹炼模式数据库,减少人为干预偏差
图片
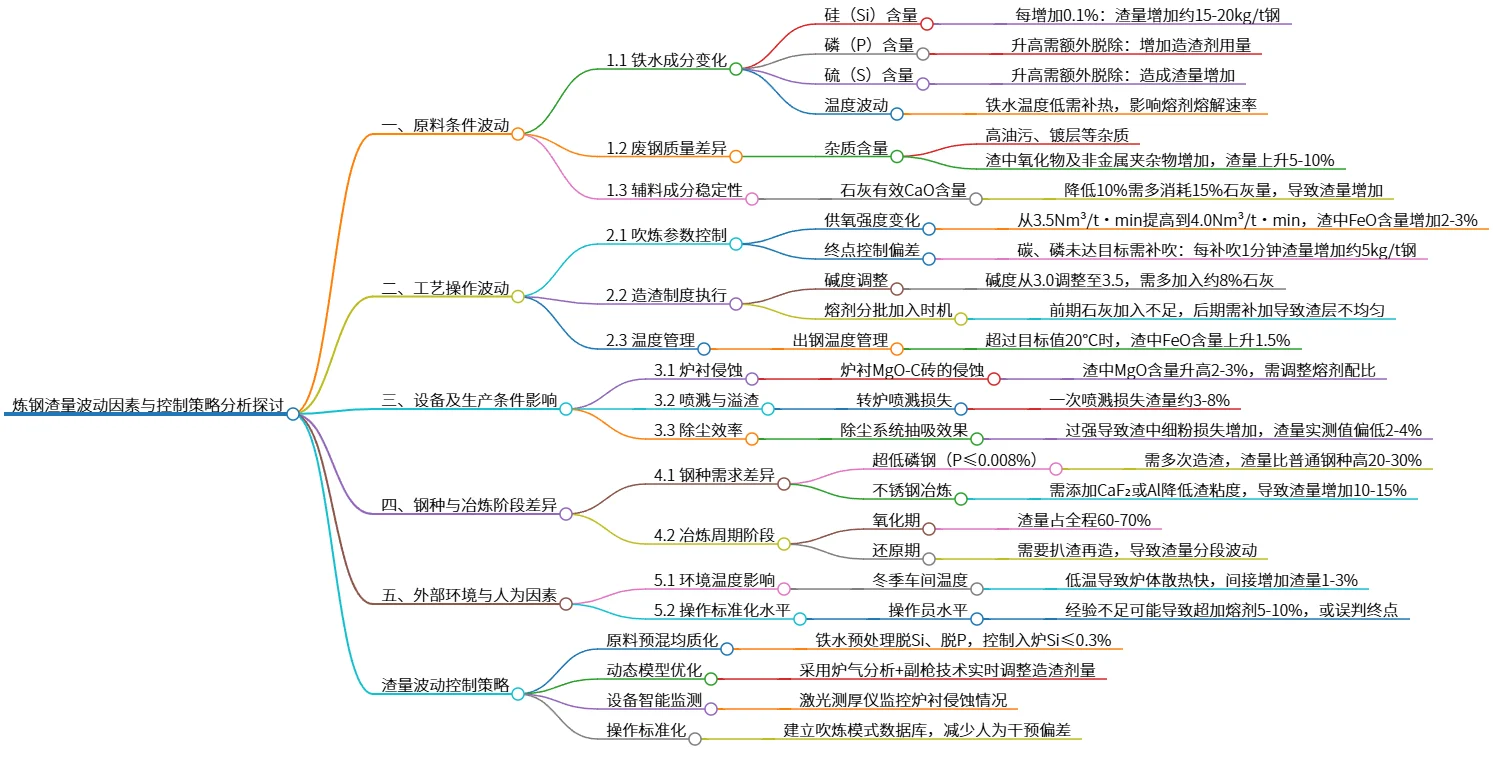